Innovative solution for medical and pharmaceutical products
MULTIVAC packaging line with six-axis kinematics for the first time
With the GMP-compliant RX 4.0 thermoformer packaging machine, MULTIVAC is setting new standards in the medical and pharmaceutical industry. For the first time, a Yaskawa six-axis robot, also GMP-compliant, is used at the end of the line. This brings many advantages, but in particular a decisive plus in flexibility.
- Industrias
- Automatización de laboratorios
- Packaging
- Aplicaciones
- Envase y Embalaje
- Cliente
- MULTIVAC Sepp Haggenmüller SE & Co. KG
- Productos
- Serie HD
The MULTIVAC Group, based in Wolfertschwenden, Germany, has made a name for itself with application-specific packaging solutions in the pharmaceutical, medical and food industries. The portfolio of the company, which was founded in 1961 and has around 7,400 employees, includes various packaging technologies, automation solutions, labeling and inspection systems and, last but not least, packaging materials.
The growing demands for process accuracy and reproducibility in the medical and pharmaceutical industries when packaging sensitive products prompted MULTIVAC to develop a thermoformer packaging machine that meets the increased requirements of customers, the market and legislation. At the same time, the RX 4.0 machine has succeeded in reducing throughput times and maximizing production efficiency and flexibility.
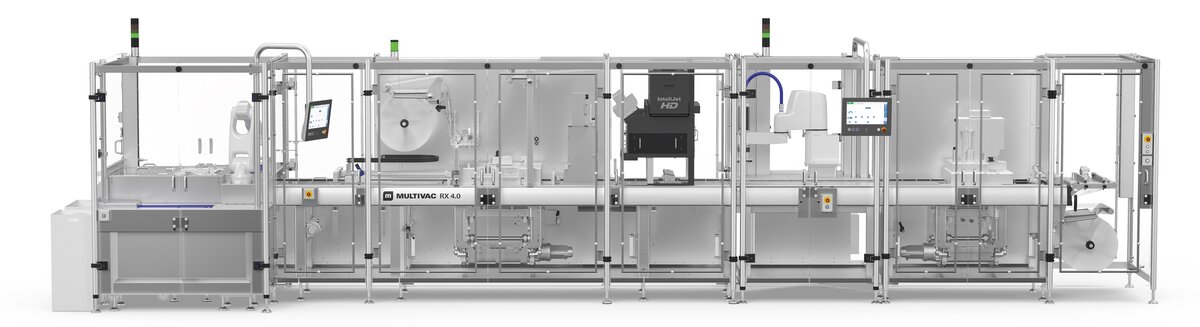
Picture: The GMP-compliant RX 4.0 thermoformer packaging machine sets new standards in the medical device and pharmaceutical industries. © MULTIVAC
Premiere: Use of a GMP-compliant six-axis robot
A new feature of the packaging machine is the use of a six-axis robot suitable for the medical and pharmaceutical sectors, the first time MULTIVAC has used a third-party product. "Developing our own six-axis kinematics would not have made sense with our existing product range. That is why we decided in favor of a robot from Yaskawa," explains Wolfgang Buchenberg, Senior Director Technics Solutions at MULTIVAC.
A look at how the machine works explains why the packaging specialist favored six-axis kinematics for the new machine. The products to be packaged are placed by a SCARA robot, a MULTIVAC in-house development, into thermoformed pack cavities formed by the thermoformer packaging machine in the first step. The RX 4.0 handles the remaining primary packaging processes, including sealing the bottom film with a top film that is printed inline in multiple colors before sealing. This is followed by visual inspection of the print image and separation of the packs by means of a full cut.
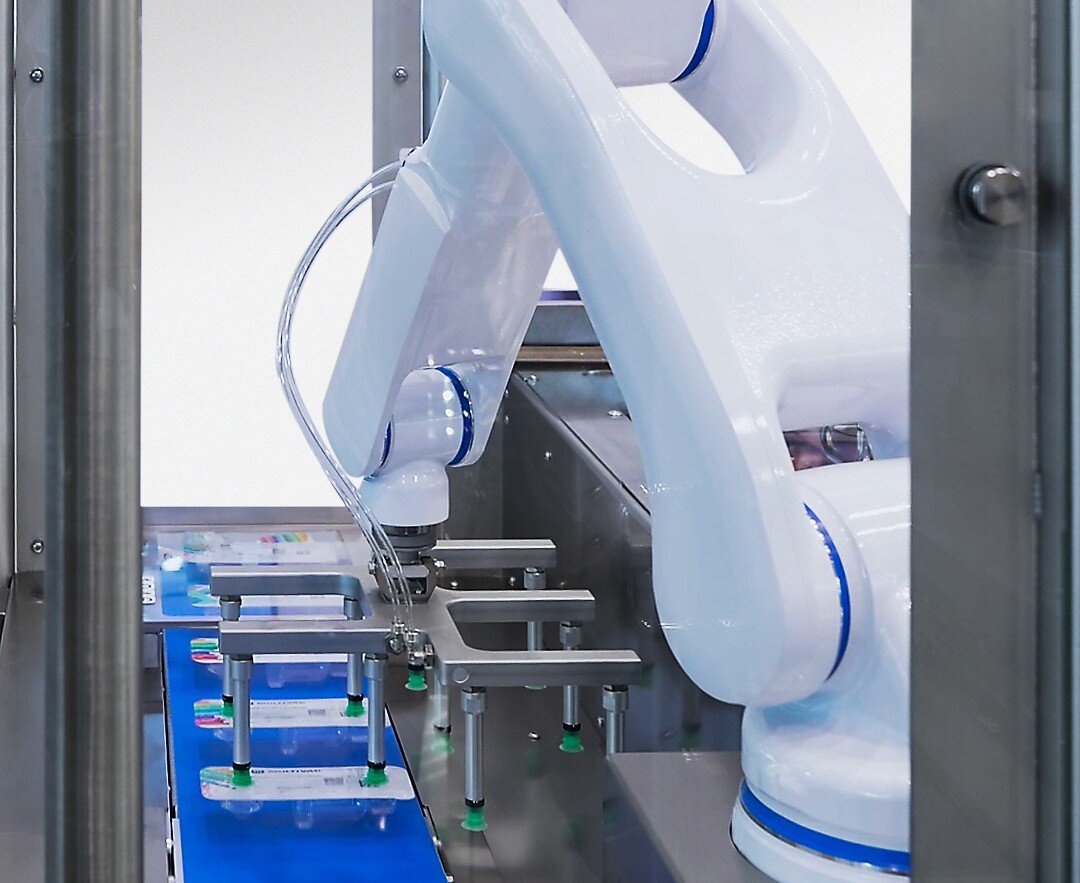
Picture: The MOTOMAN HD7 is suitable for use in cleanrooms up to the highest GMP class A. © MULTIVAC
Six axes for even more flexibility
At the output of the thermoformer packaging machine, the packs are removed directly from the cutting unit and separated by the Yaskawa robot. Wolfgang Buchenberg explains why the use of a six-axis robot is the best choice here: "Using the MOTOMAN HD7 has decisive advantages, especially in terms of flexibility. We can unload using single or multiple picks. In our demo system, for example, we use a five-pick vacuum gripper. Packs can also be separated on moving conveyors or at defined stationary positions. And thanks to the six axes, we have no limitations in terms of access to positions and can handle many different formats.
MULTIVAC's decision to use Yaskawa six-axis robots in its thermoforming packaging machines was not an easy one. On the contrary: In a detailed market study, those responsible analyzed the range of cleanroom robots offered by the five largest manufacturers, compared them on the basis of a complex requirements profile and made a well-founded decision.
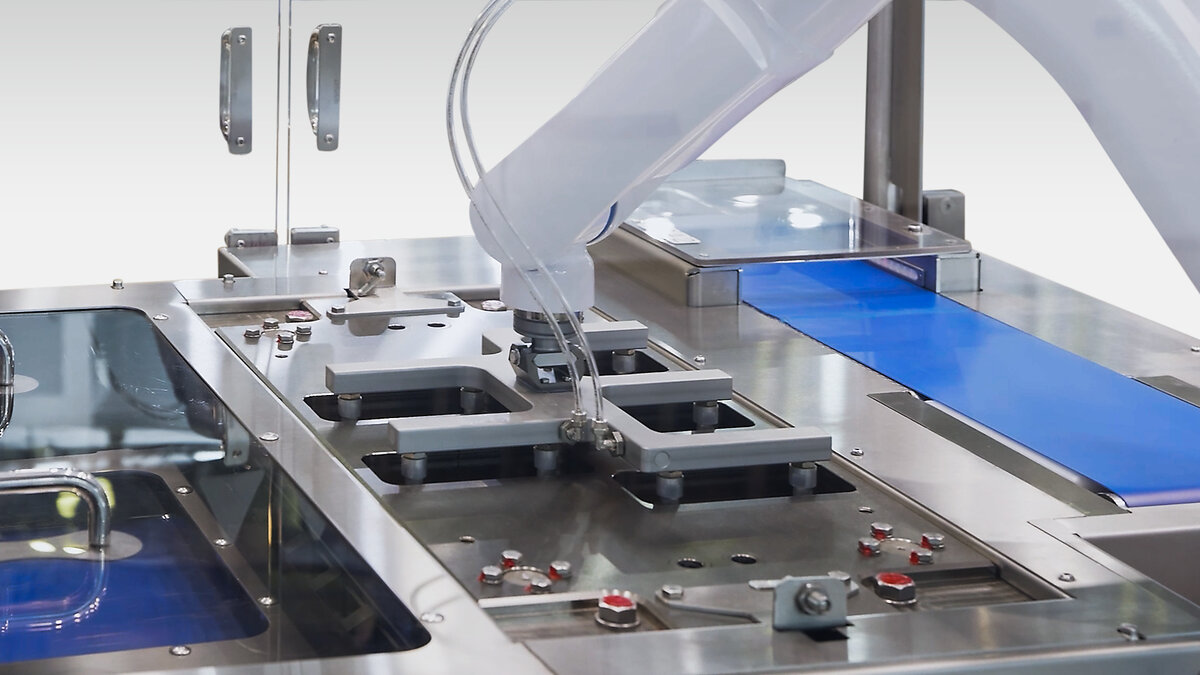
Picture: Yaskawa's HD series impresses with its reduced kinematics, which offers decisive advantages in the pharmaceutical and medical sectors. © MULTIVAC
A European development for all types of cleanrooms
The winner of the selection process was the MOTOMAN HD7 from Japanese supplier Yaskawa. This high-performance robot is a new European development for sensitive applications, created in close cooperation with the Fraunhofer Institute for Manufacturing Engineering and Automation IPA. Like its bigger brother, the MOTOMAN HD8, the MOTOMAN HD7 is suitable for use in cleanrooms from class ISO 5 up to the highest GMP class A. It therefore fulfills the requirements that MULTIVAC places on the cleanroom suitability of its robots in every respect.
But the GMP-compliant and cleanroom-compatible design was only one of many aspects that influenced the decision in favor of Yaskawa. Wolfgang Buchenberg comments: "For MULTIVAC, the issue of control technology and integration is also of crucial importance. The Yaskawa 'MotoLogix' software interface allows MOTOMAN kinematics, including cobots, to be seamlessly integrated into the MULTIVAC control and software platform, which also ensures centralized line operation from a single source for six-axis robots.
The Yaskawa HD series also features a reduced kinematics design, which offers significant advantages in the pharmaceutical and medical sectors. The routing of cables and connections within the arm, low particle generation and FDA compliance ensure the necessary customer acceptance and facilitate key requirements such as easy cable routing.
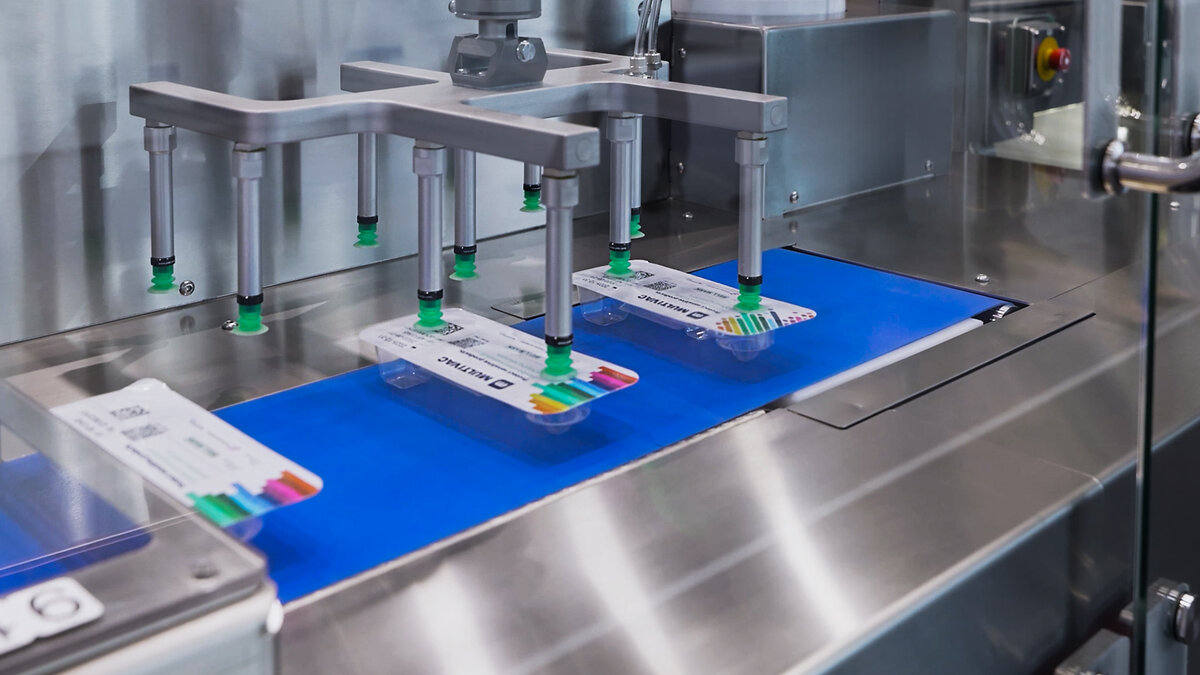
Picture: The MOTOMAN HD7 removes and deposits the packs at the output of the thermoformer packagine machine. © MULTIVAC
Setting new standards: the RX 4.0 thermoformer packaging machine
All in all, with the new RX 4.0 thermoformer packagine machine and the first-time integration of a Yaskawa six-axis machine, MULTIVAC has succeeded in launching a customized solution for the pharmaceutical and medical sector. This solution is equally suitable for applications in primary, secondary and tertiary packaging. Sterile medical products such as implants, catheters, sutures, needles and pharmaceutical syringes, vials, ampoules, pens, injectors and combinations thereof can be packaged reliably, economically and sustainably in small and large batches with the RX 4.0.
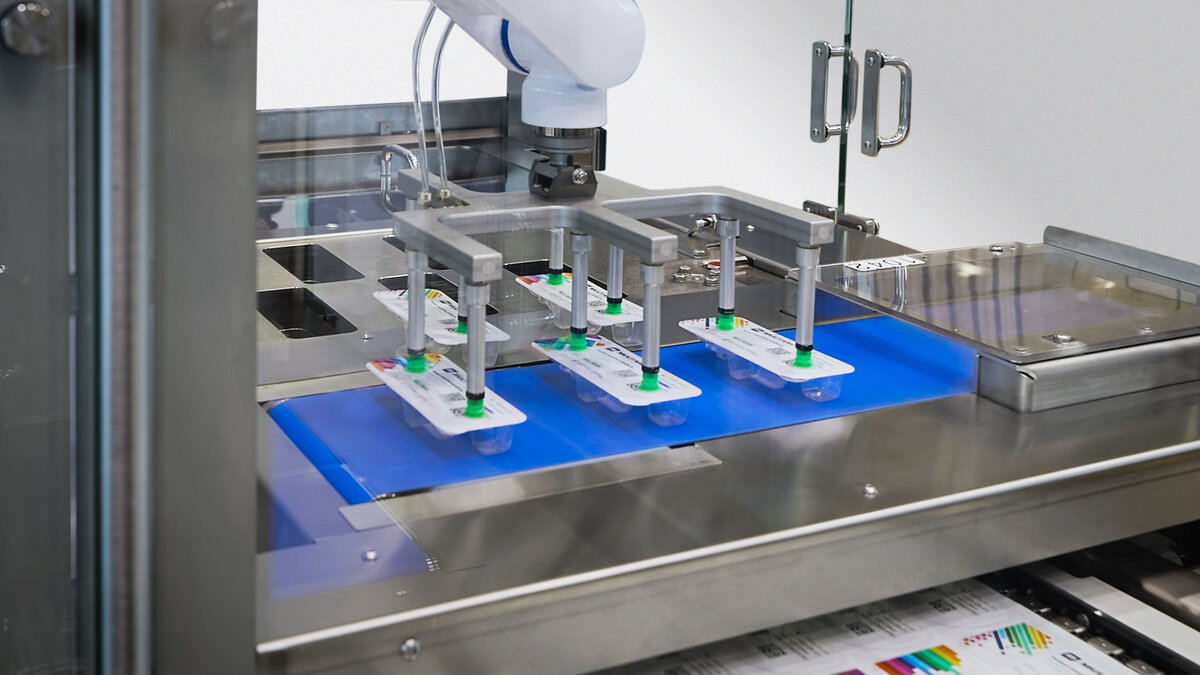
Picture: In principle, unloading can be based on single or multiple picks; the demo system uses a quintuple vacuum gripper. © MULTIVAC
"With this line and its end-to-end sensor-controlled packaging process, we are achieving a new level of process accuracy and reproducibility. Thanks to consistent data acquisition and evaluation, the machine can parameterize itself close to the optimum operating point and automatically correct itself in the event of deviations from the target. In addition, we can optimally meet the requirements of the medical and pharmaceutical industry thanks to the simple operation, fast changeover, optimized sealing process and the first-time use of the Yaskawa robot," says Wolfgang Buchenberg.
Text: Ralf Högel